What Can Companies Do To Avoid Product Recalls?
- Antel Solutions
- Apr 25, 2024
- 3 min read
Product recalls can be a major headache for businesses, not to mention costly and damaging to your reputation. A product recall happens when a company discovers that one of its products is unsafe or otherwise fails to meet certain standards. Prompting them to reach out to customers to return the product, often in exchange for a refund, replacement or repair.
The product recall process typically follows several steps:
Identification of the Issue: The problem with the product is identified either through internal testing, customer complaints or external investigations.
Notification: The company notifies the relevant authorities and the public about the issue and initiates the recall process.
Removal: The product is removed from sale and distribution channels.
Rectification: The product is fixed, replaced or refunded to customers.
Evaluation: The company evaluates the recall process to improve future operations and avoid similar issues going forward.
Strategies to Avoid Product Recalls
1. Improved Quality Control
Quality control is the cornerstone of product safety. By strengthening quality control processes, companies can detect and manage potential problems before products hit the market. Techniques to improve quality control include:
Strict Standards: Implementing rigorous quality standards that exceed regulatory requirements helps ensure that products are safe and meet quality standards. By setting and adhering to high standards, companies can minimise the risk of defects and increase customer satisfaction.
Regular Audits: Conduct frequent quality audits throughout the production process to ensure standards are met consistently. This enables your business to identify and rectify deviations from quality norms before products reach your customers. These audits can be scheduled and surprise checks, ensuring that all batches maintain the highest quality level.
Adequate Employee Training: Regular training for employees can highlight quality control procedures and the importance of adhering to them. Training helps employees understand their direct impact on product quality and safety, fostering a culture of responsibility and attention to detail in the workplace.
2. Better Supply Chain Management
A product's quality is only as good as the quality of its components. Improved supply chain management ensures that every part of the product meets your company’s standards. Strategies include:
Supplier Vetting: Thoroughly vetting suppliers and choosing only those who comply with regulations and deliver high-quality materials ensures that the components used in manufacturing are reliable. This in turn, directly influences the final product's quality. This vetting process often includes checks on the supplier's financial stability, compliance history, and ability to consistently meet supply demands.
Transparent Communication: Establishing clear and open communication lines with suppliers to quickly address any issues is important. This ensures that any potential disruptions are managed proactively.
Continuous Monitoring: Regularly monitoring suppliers and their compliance with quality and safety standards guarantees that suppliers adhere to agreed-upon criteria. Continuous monitoring can involve regular site visits, product sampling and review meetings.
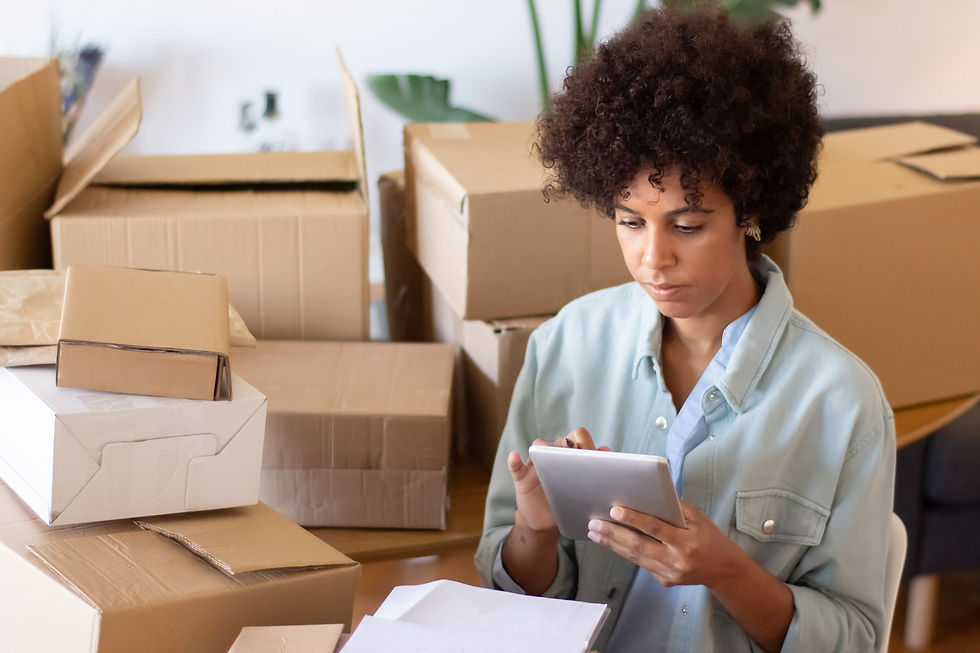
3. Rigorous Product Testing
Before launching a product, thorough testing is essential to catch any potential safety issues. Effective product testing involves:
Pre-market Testing: Extensive testing should take place before the product is available to the public to confirm it is safe and functions as intended. This is a critical phase that helps prevent potential failures or safety issues from reaching consumers. This testing can range from laboratory testing, field trials and user testing groups, which help to identify design flaws and usability issues.
Ongoing Testing: Continuously testing products even after they are on the market to identify potential long-term issues that may not be apparent initially helps maintain the integrity of products throughout their lifecycle. This approach includes regular checks and using customer feedback as a valuable tool for detecting problems.
Third-Party Verification: Using independent bodies to test product quality can provide an unbiased view of a product’s safety and effectiveness. Third-party verification by an external expert organisation helps to validate the company's internal results and builds consumer trust by showing that the product meets or exceeds industry standards.
4. Implementing Feedback Mechanisms
A robust system for gathering and analysing customer feedback can alert your business to potential product defects before they escalate into a recall. This includes:
Active Listening Tools: Using tools such as social media listening and customer surveys to gather feedback.
Rapid Response Teams: Having teams in place to respond quickly to product issues reported by customers.
Data Analysis: Employing advanced data analysis to detect patterns in customer feedback that could indicate a widespread problem.
By implementing sound strategies, your company can drastically reduce the chances of ever having to issue a product recall. This can save your company time and money while also protecting customers from potential harm. If you want to ensure that your company is taking all the necessary measures to avoid product recalls, don't hesitate to contact Antel Solutions. Reach out to us today, or browse our website for more information.
Comments